Titanium (Ti) has revolutionized the dental industry with its exceptional properties, making it a top choice for metal-based frameworks. Its lightweight nature, superior biocompatibility, and corrosion resistance have set a new standard for dental prostheses. This article delves into the properties, manufacturing methods, clinical applications, and current trends of titanium in dentistry, offering valuable insights for dental practices aiming to enhance their solutions.
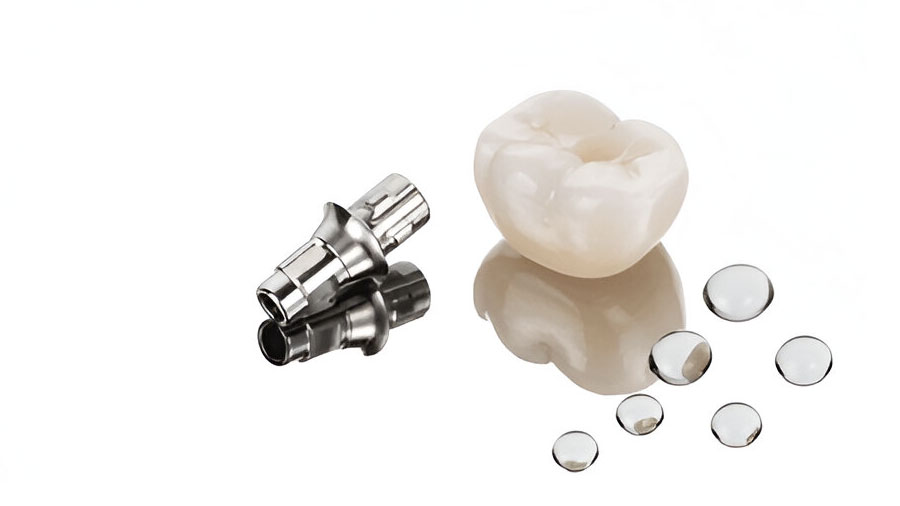
Table of contents [Show]
- Properties and Characteristics of Titanium
- Manufacturing Methods for Titanium Frameworks
- Types of Titanium Used in Dentistry
- Clinical Applications of Titanium Frameworks
- Advantages of Titanium Frameworks
- Challenges and Considerations
- Current Trends and Future Directions
- Biological Effects of Titanium
- Why Choose XDENT LAB for Titanium Frameworks?
- Conclusion
Properties and Characteristics of Titanium
Titanium and its alloys possess unique properties that make them ideal for dental frameworks:
High Corrosion Resistance: Titanium resists degradation in the oral environment, ensuring long-term stability.
Excellent Biocompatibility: Well-tolerated by human tissues, with minimal risk of allergic reactions or inflammation.
Lightweight: Titanium frameworks are about 400% lighter than traditional materials like cobalt-chromium, improving patient comfort.
Acceptable Mechanical Strength: Strong enough for load-bearing dental applications such as bridges and implant frameworks.
Favorable Modulus of Elasticity: Closer to bone than other metals, reducing stress shielding and enhancing osseointegration.
These characteristics make titanium a versatile and reliable material for modern dental frameworks.
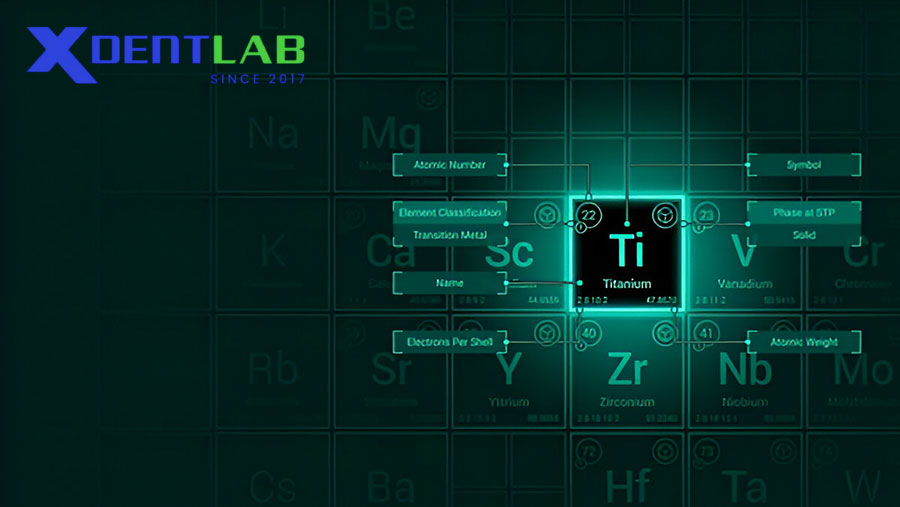
Manufacturing Methods for Titanium Frameworks
Titanium frameworks can be fabricated using various techniques, each offering distinct advantages:
CAD-CAM Milling
Overview: Computer-aided design and manufacturing (CAD-CAM) technology mills frameworks from titanium blocks.
Advantages: High precision, consistent quality, and excellent fit.
Applications: Ideal for crowns, bridges, and removable partial dentures (RPDs).
Overview: An additive manufacturing technique that builds frameworks layer by layer using a laser to sinter titanium powder.
Advantages: Allows for complex geometries, reduced material waste, and excellent mechanical properties.
Applications: Particularly suited for implant-supported prostheses and hybrid dentures.
Traditional Casting
Overview: A less common method for titanium due to its high melting point (1668°C) and reactive nature.
Challenges: Requires specialized equipment and controlled environments, making it less cost-effective.
CAD-CAM vs. DMLS
Studies comparing CAD-CAM and DMLS have shown that both methods offer superior precision and mechanical performance compared to traditional casting. However, DMLS is particularly advantageous for creating intricate designs and frameworks for complex cases.
Types of Titanium Used in Dentistry
Titanium is available in various forms to meet specific dental requirements:
Commercially Pure (CP) Titanium
Grades: Ranges from Grade 1 (softest) to Grade 4 (strongest).
Applications: Commonly used for crowns, bridges, and removable frameworks.
Titanium Alloys
Examples: Ti-6Al-4V (titanium, aluminum, vanadium) is a popular alloy due to its enhanced strength and corrosion resistance.
Applications: Frequently used for implant-supported prostheses.
Surface-Modified Titanium
Purpose: Enhanced with surface treatments to improve osseointegration and biological responses.
Applications: Ideal for implants and frameworks requiring superior tissue integration.
Clinical Applications of Titanium Frameworks
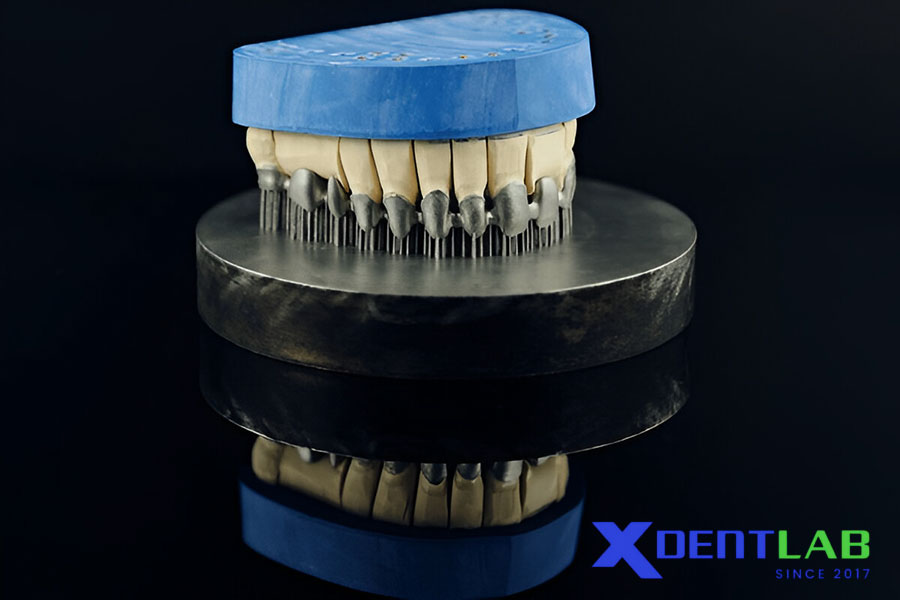
Titanium frameworks are extensively used in various dental prostheses due to their versatility and performance:
Removable Partial Dentures (RPDs)
Benefits: Lightweight and comfortable for patients, reducing tongue and tissue irritation.
Clinical Performance: Comparable to traditional materials with the added advantage of weight reduction.
Implant-Supported Prostheses
Applications: Particularly effective for hybrid dentures and full-arch restorations.
Advantages: Superior biocompatibility and long-term stability in osseointegrated implants.
Fixed Dental Prostheses
Examples: Crowns, bridges, and full-arch frameworks.
Advantages: High precision and durability, with excellent aesthetic outcomes when veneered.
Maxillofacial Prostheses
Applications: Used for reconstructive procedures due to titanium’s biocompatibility and lightweight nature.
Advantages of Titanium Frameworks
Titanium frameworks offer numerous benefits that make them a preferred choice in dentistry:
Key Benefits
Weight Reduction: Significantly lighter than cobalt-chromium and other metals, improving patient comfort.
Biocompatibility: Minimal risk of allergic reactions or tissue irritation, making it ideal for patients with metal sensitivities.
Durability: Resistant to corrosion and wear, ensuring long-term stability in the oral environment.
Precision: Modern manufacturing methods allow for highly accurate and well-fitting frameworks.
Clinical Performance
Patients report improved comfort due to titanium’s lightweight nature.
Reduced risk of irritation and inflammation compared to traditional metal frameworks.
Excellent for patients with metal allergies or sensitivities.
Challenges and Considerations
While titanium offers numerous advantages, there are some challenges and considerations to keep in mind:
Technical Challenges
High Melting Point: Makes traditional casting difficult and costly.
Reactive Nature: Requires specialized equipment and controlled environments during processing.
Higher Initial Cost: Titanium frameworks may have a higher upfront cost compared to alternatives like cobalt-chromium.
Clinical Considerations
Elastic Modulus: Lower than cobalt-chromium, which may affect rigidity in certain applications.
Surface Finishing: More challenging compared to other metals, requiring expertise for optimal results.
Color: Titanium’s gray color may show through thin ceramic veneers, affecting aesthetics.
Current Trends and Future Directions
The use of titanium in dental frameworks continues to evolve with advancements in technology and materials science:
Advanced Manufacturing Processes
Improved cost-effectiveness through innovations in CAD-CAM and DMLS technologies.
New Titanium Alloys
Development of alloys with enhanced mechanical properties and biocompatibility.
Innovative Surface Modifications
Research into surface treatments to improve osseointegration and biological responses.
Integration with Digital Dentistry
Seamless workflows combining digital scanning, design, and manufacturing for faster and more accurate results.
Biological Effects of Titanium
Titanium’s biological properties make it an excellent choice for dental frameworks:
Tissue Compatibility: Minimal ion release compared to other metals, reducing the risk of adverse reactions.
Stable Oxide Layer: Prevents corrosion and enhances biocompatibility.
Alloy Composition Impact: Biological effects vary depending on the specific titanium alloy and surface treatment used.
Why Choose XDENT LAB for Titanium Frameworks?
At XDENT LAB, we specialize in manufacturing high-quality titanium frameworks tailored to meet the needs of dental practices. With advanced CAD-CAM and DMLS technologies, FDA-approved processes, and a team of skilled technicians, we deliver reliable and precise solutions for your patients.
What We Offer
Expertise: Over 6 years of experience in Lab-to-Lab dental outsourcing services.
State-of-the-Art Technology: Leveraging the latest manufacturing techniques for superior results.
Compliance: Meeting U.S. market standards with FDA and ISO certifications.
Customized Solutions: Tailored frameworks for fixed and removable prostheses.
Conclusion
Titanium has emerged as a game-changer in dental frameworks, offering unmatched biocompatibility, lightweight comfort, and long-term durability. With advancements in manufacturing methods and surface modifications, titanium continues to set new standards in dental prosthetics.
Partner with XDENT LAB to access cutting-edge titanium framework solutions that combine innovation, precision, and reliability. Let us help you deliver superior outcomes for your dental practice and patients.
XDENT LAB is an expert in Lab-to-Lab Full Service from Vietnam, with the signature services of Removable & Implant, meeting U.S. market standards – approved by FDA & ISO. Founded in 2017, XDENT LAB has grown from local root to global reach, scaling with 2 factories and over 100 employees.. Our state-of-the-art technology, certified technicians, and commitment to compliance make us the trusted choice for dental practices looking to ensure quality and consistency in their products.
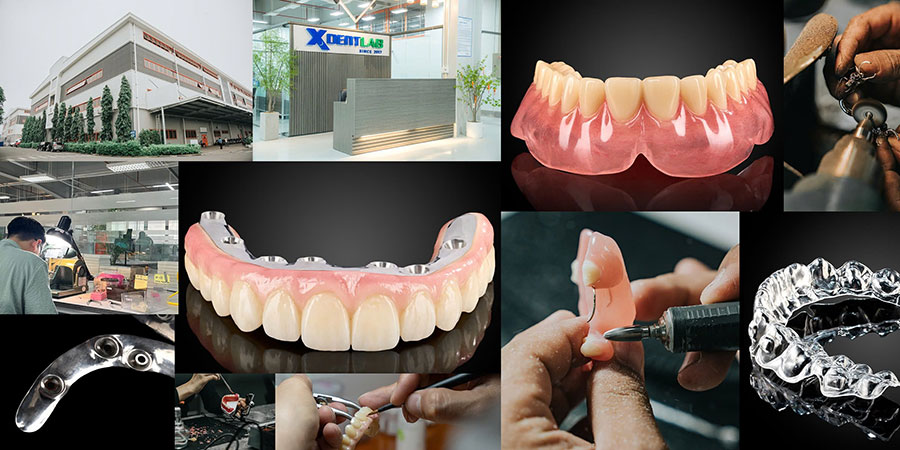
Our commitments are:
100% FDA-Approved Materials.
Large-Scale Manufacturing, high volume, remake rate < 1%.
2~3 days in lab (*digital file).
Your cost savings 30%.
Uninterrupted Manufacturing 365 days a year.
Contact us today to establish a strategy to reduce operating costs.
--------❃--------
Vietnam Dental Laboratory - XDENT LAB
🏢 Factory 1: 95/6 Tran Van Kieu Street, Binh Phu Ward, Ho Chi Minh City, Vietnam
🏢 Factory 2: Kizuna 3 Industrial Park, Can Giuoc Commune, Tay Ninh Province, Vietnam
☎ Hotline: 0919 796 718 📰 Get detailed pricing