Cobalt-Chromium (Co-Cr) alloys are among the most widely used materials in dentistry for metal-based frameworks. Known for their excellent mechanical properties, corrosion resistance, and cost-effectiveness, Co-Cr alloys are integral to the fabrication of fixed and removable dental prostheses. This article explores the composition, manufacturing methods, mechanical properties, biocompatibility considerations, clinical applications, and advantages of Co-Cr frameworks, providing valuable insights for dental practices looking to optimize their solutions.
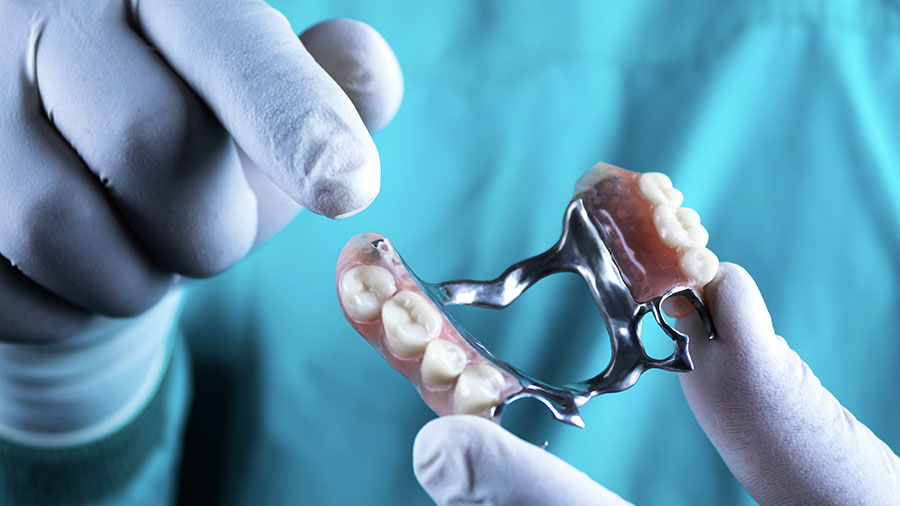
Table of contents [Show]
Composition and Properties
Cobalt-Chromium alloys used in dental frameworks typically consist of:
53-67% Cobalt (Co): Provides strength and durability.
25-32% Chromium (Cr): Enhances corrosion resistance.
2-6% Molybdenum (Mo): Improves wear resistance and mechanical properties.
Small amounts of other elements: May include nickel, iron, or silicon for specific enhancements.
Key Features
Mechanical Excellence: High elastic modulus, wear resistance, and fatigue strength make Co-Cr alloys ideal for dental prostheses.
Corrosion Resistance: Chromium forms a passive oxide layer, protecting the alloy from environmental degradation.
Biocompatibility: Widely used in both dental frameworks and orthopedic implants due to their compatibility with human tissues.
Manufacturing Methods
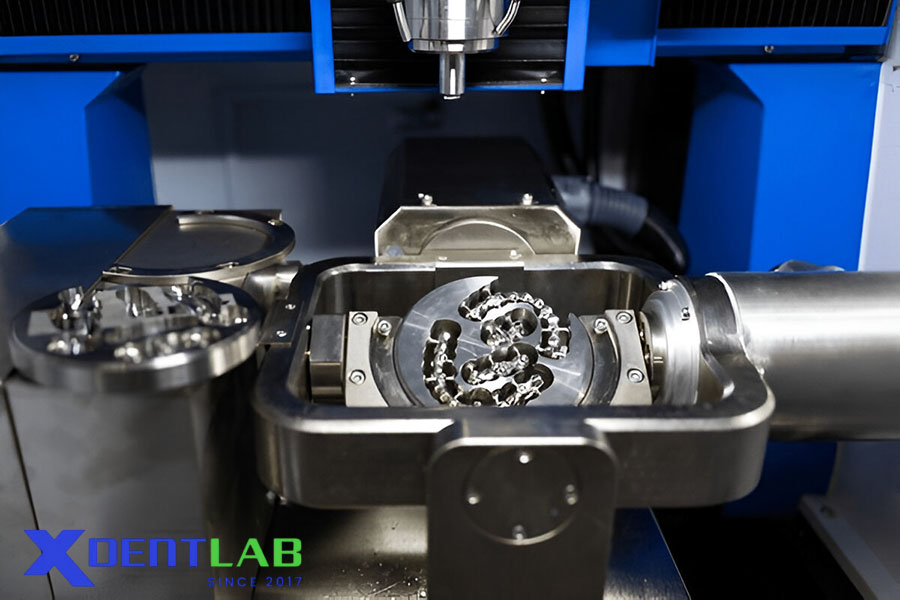
Co-Cr dental frameworks can be fabricated using various techniques, each offering unique benefits and limitations:
Traditional Casting
Overview: A time-tested method involving the use of wax patterns and investment casting.
Advantages: Cost-effective and widely available.
Limitations: May result in porosity and variability in mechanical properties.
CAD-CAM Milling
Overview: Computer-aided design and manufacturing (CAD-CAM) technology produces frameworks from pre-sintered Co-Cr blocks.
Advantages: Precision, consistency, and superior fit compared to traditional casting.
Limitations: Higher initial investment in equipment.
Selective Laser Melting (SLM)
Overview: A modern additive manufacturing technique that uses laser sintering to build frameworks layer by layer.
Advantages: Allows for complex designs, reduced material waste, and enhanced mechanical properties.
Limitations: Requires advanced equipment and expertise.
Impact of Manufacturing Methods
Recent studies have shown that the choice of manufacturing method significantly affects the microstructure and mechanical properties of Co-Cr frameworks. CAD-CAM and SLM techniques generally produce frameworks with better mechanical performance and reduced variability compared to traditional casting.
Mechanical Properties
Co-Cr alloys are renowned for their:
Mechanical Strength: Suitable for high-load applications in dental prostheses.
Wear Resistance: Ensures long-term durability, even under occlusal forces.
Corrosion Resistance: Chromium content provides excellent protection against oral fluids and environmental factors.
Fatigue Resistance: Ideal for frameworks subjected to repeated stress, such as removable partial dentures (RPDs).
Studies comparing frameworks produced by different methods have highlighted the superior mechanical properties of CAD-CAM and SLM-fabricated Co-Cr frameworks, making them preferred choices for modern dental practices.
Biocompatibility Considerations
While Co-Cr alloys are widely used, their biocompatibility is influenced by several factors:
Potential Risks: Co-Cr alloys may release cobalt, chromium, and molybdenum ions, which can cause inflammatory reactions, tissue discoloration, or hyperplasia in sensitive patients.
Manufacturing Impact: The extent of metal ion release depends on the fabrication method, with CAD-CAM and SLM techniques generally resulting in lower release levels.
Passivation Behavior
Protective Layer: Co-Cr alloys exhibit passivation, forming a protective oxide layer that minimizes metal ion release and enhances biocompatibility.
Finishing and Polishing
Proper finishing and polishing are critical to reducing metal ion release and improving tissue compatibility. Smooth surfaces help minimize plaque accumulation and irritation.
Clinical Applications
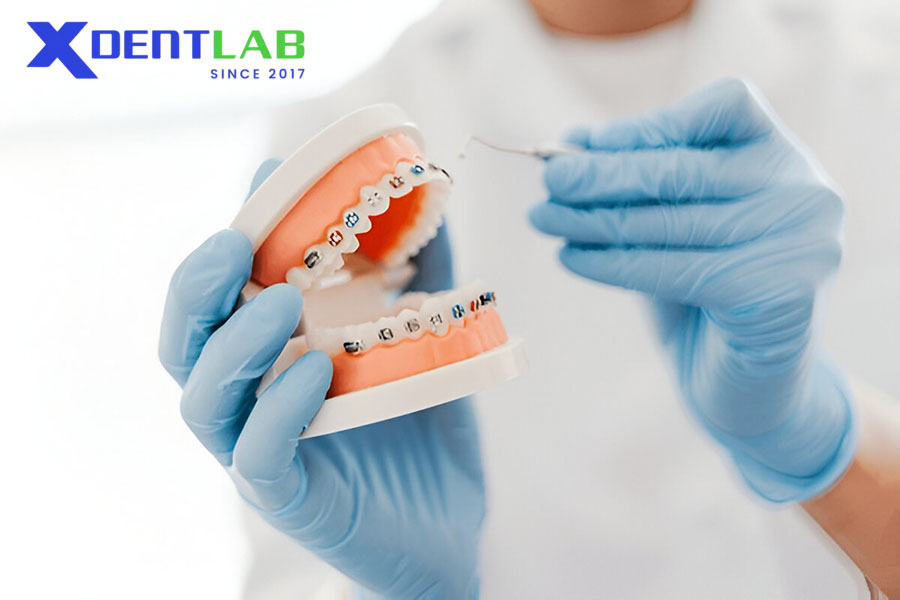
Co-Cr alloys are versatile materials used in a variety of dental frameworks, including:
Fixed Partial Dentures (FPDs)
Strength and Durability: Ideal for posterior bridges requiring high-load resistance.
Manufacturing Options: CAD-CAM and SLM techniques offer superior fit and mechanical properties.
Removable Partial Dentures (RPDs)
Cost-Effectiveness: Co-Cr’s affordability makes it the dominant choice for RPD frameworks.
Metal-Free Alternatives: PEEK is gaining popularity for patients with metal allergies.
Implant Frameworks
Precision and Longevity: Co-Cr frameworks fabricated using CAD-CAM or SLM provide excellent fit and durability for implant-supported prostheses.
Crown and Bridge Frameworks
Versatility: Suitable for both anterior and posterior regions, with aesthetic enhancements using veneering materials.
Advantages and Considerations
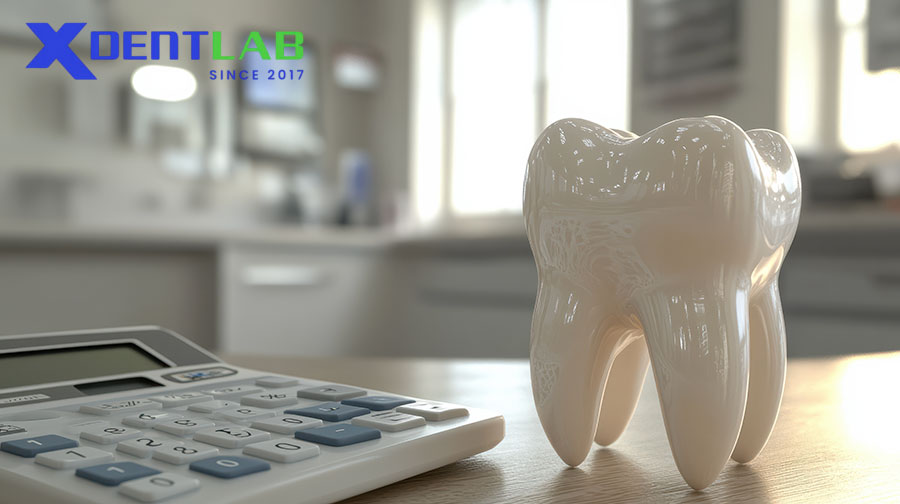
Advantages
Cost-Effective: A budget-friendly alternative to noble metal alloys.
Mechanical Excellence: High strength, wear resistance, and fatigue resistance ensure long-term performance.
Versatility: Suitable for both fixed and removable prostheses.
Proven Clinical Performance: Widely used in dentistry with a strong track record of success.
Considerations
Allergic Reactions: Metal ion release may cause sensitivity in some patients.
Manufacturing Impact: The choice of fabrication method affects final properties, with CAD-CAM and SLM offering better outcomes.
Finishing Requirements: Proper polishing is essential for optimal biocompatibility and performance.
XDENT LAB: Your Partner for Co-Cr Framework Solutions
At XDENT LAB, we specialize in manufacturing high-quality Co-Cr frameworks using advanced technologies like CAD-CAM milling and Selective Laser Melting (SLM). With FDA and ISO certifications, state-of-the-art equipment, and a team of over 100 skilled technicians, we deliver reliable and consistent solutions for dental practices worldwide.
Why Choose XDENT LAB?
Expertise: Over 6 years of experience in Lab-to-Lab dental outsourcing services.
Precision Manufacturing: Leveraging CAD-CAM and SLM technologies for superior frameworks.
Compliance: Meeting U.S. market standards with FDA-approved processes.
Customized Solutions: Tailored frameworks for fixed and removable prostheses.
Conclusion
Cobalt-Chromium (Co-Cr) alloys remain a cornerstone of metal-based frameworks in dentistry, offering exceptional mechanical properties, corrosion resistance, and cost-effectiveness. The choice of manufacturing method—whether traditional casting, CAD-CAM milling, or SLM—significantly impacts the microstructure, mechanical performance, and biocompatibility of the final product.
Partner with XDENT LAB to access cutting-edge Co-Cr framework solutions that combine innovation, quality, and reliability. Let us help you deliver superior outcomes for your dental practice and patients.
XDENT LAB is an expert in Lab-to-Lab Full Service from Vietnam, with the signature services of Removable & Implant, meeting U.S. market standards – approved by FDA & ISO. Founded in 2017, XDENT LAB has grown from local root to global reach, scaling with 2 factories and over 100 employees.. Our state-of-the-art technology, certified technicians, and commitment to compliance make us the trusted choice for dental practices looking to ensure quality and consistency in their products.
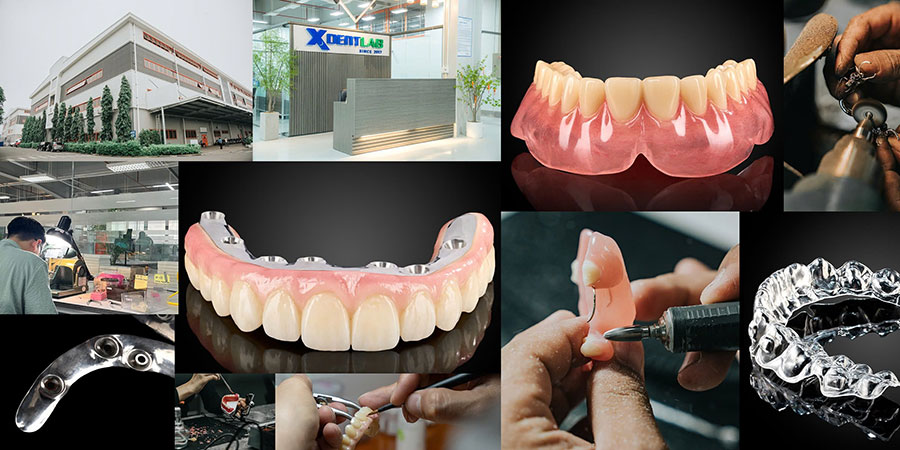
Our commitments are:
100% FDA-Approved Materials.
Large-Scale Manufacturing, high volume, remake rate < 1%.
2~3 days in lab (*digital file).
Your cost savings 30%.
Uninterrupted Manufacturing 365 days a year.
Contact us today to establish a strategy to reduce operating costs.
--------❃--------
Vietnam Dental Laboratory - XDENT LAB
🏢 Factory 1: 95/6 Tran Van Kieu Street, Binh Phu Ward, Ho Chi Minh City, Vietnam
🏢 Factory 2: Kizuna 3 Industrial Park, Can Giuoc Commune, Tay Ninh Province, Vietnam
☎ Hotline: 0919 796 718 📰 Get detailed pricing